Before You Buy Greenhouse Software: What Multi-Site Growers Overlook About Mobile Inventory Access
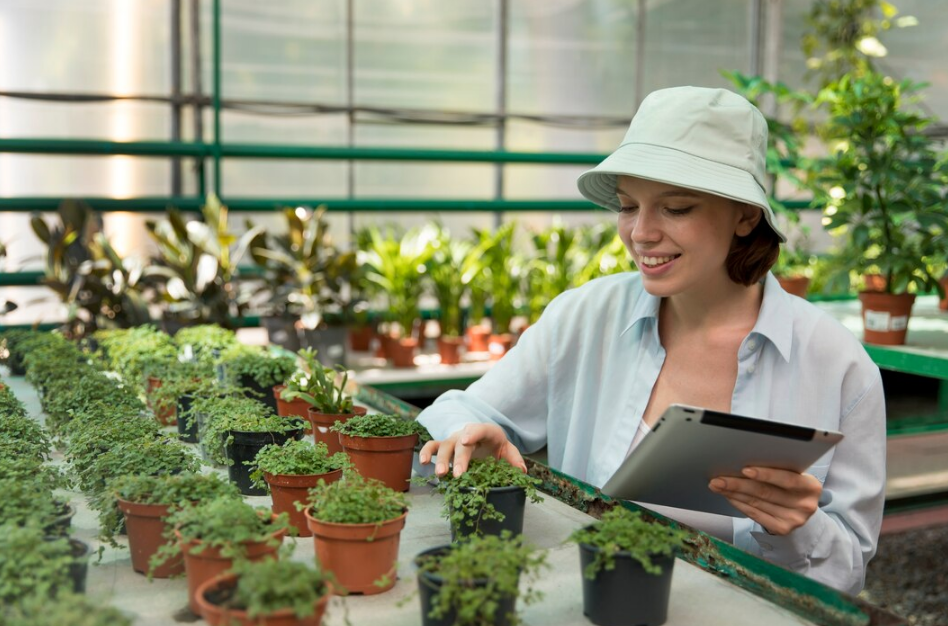
Many greenhouse managers require more robust tools for production, inventory, and shipping. They check features, prices, and reports. However, one key aspect often overlooked is mobile inventory access. For growers running multiple sites, this feature can prevent daily errors that cost time and money.
When you buy greenhouse software, you likely consider production tracking, order management, and accounting. But without live mobile access, staff can’t keep up with racks and trays moving across multiple sites. This gap creates outdated data, delays, and lost sales.
Why Mobile Tools Matter For Big Growers
Picture a grower with three greenhouses in one region. Each site grows different plants and shifts racks around daily. If workers can’t update counts on the spot, the data goes stale fast. Teams waste time calling each other or making guesses.
Strong greenhouse inventory apps give staff mobile access to live numbers. Workers use phones or tablets to scan trays, update counts, and correct errors before they escalate into larger issues. This means managers know what they have and where it is.
Small Mistakes Add Up Fast
When workers can’t update data in real-time, they write notes or make updates later. This leads to double entries and missing racks. A delivery may go out short, or a batch may ship from the wrong site. Correcting these mistakes incurs additional expenses and erodes customer trust.
With mobile tools, staff keep everyone on the same page. The whole team uses the same numbers, not guesses scribbled on paper.
Real-Life Ways Mobile Access Helps
Mobile access does more than fix counts. For example:
- A manager walks the greenhouse to check plant readiness. They see some plants ready for shipment a week early. With mobile tools, they update quantities on the spot, allowing the sales team to fill unexpected orders.
- A crew shifts racks from propagation to finishing at another site. They scan the trays before loading them, so inventory numbers are adjusted immediately. The receiving site knows what is coming before the truck arrives.
- A customer calls to ask about the order status. Instead of calling around, your team looks up live data from any device to confirm how many racks are ready and where they are.
Without mobile tools, each step would require more calls and increase the room for error.
Look For Offline Options
Some greenhouses have weak Wi-Fi. Good greenhouse inventory apps also work offline. Staff can scan racks or adjust counts without losing data if the signal drops. The system syncs once the connection comes back.
This stops lost scans and wrong numbers when workers move between greenhouses or fields.
Barcodes And Scanning Speed
Mobile tools should handle barcode scanning easily. Many nurseries use serialized trays. Fast, simple scanning keeps inventory up to date without manual data entry.
When you buy greenhouse software, check that scanning is smooth. Staff should not waste time typing numbers for every rack. This slows work and causes mistakes.
Reduce Plant Loss
Mobile updates enable growers to maintain better control over their plants at each stage. If something goes wrong on one site, managers shift healthy plants to other orders or locations. Slow updates make that harder.
Many greenhouse managers require more robust tools for production, inventory, and shipping. They check features, prices, and reports. However, one key aspect often overlooked is mobile inventory access. For growers running multiple sites, this feature can prevent daily errors that cost time and money.
When you buy greenhouse software, you likely consider production tracking, order management, and accounting. But without live mobile access, staff can’t keep up with racks and trays moving across multiple sites. This gap creates outdated data, delays, and lost sales.
Why Mobile Tools Matter For Big Growers
Picture a grower with three greenhouses in one region. Each site grows different plants and shifts racks around daily. If workers can’t update counts on the spot, the data goes stale fast. Teams waste time calling each other or making guesses.
Strong greenhouse inventory apps give staff mobile access to live numbers. Workers use phones or tablets to scan trays, update counts, and correct errors before they escalate into larger issues. This means managers know what they have and where it is.
Small Mistakes Add Up Fast
When workers can’t update data in real-time, they write notes or make updates later. This leads to double entries and missing racks. A delivery may go out short, or a batch may ship from the wrong site. Correcting these mistakes incurs additional expenses and erodes customer trust.
With mobile tools, staff keep everyone on the same page. The whole team uses the same numbers, not guesses scribbled on paper.
Real-Life Ways Mobile Access Helps
Mobile access does more than fix counts. For example:
- A manager walks the greenhouse to check plant readiness. They see some plants ready for shipment a week early. With mobile tools, they update quantities on the spot, allowing the sales team to fill unexpected orders.
- A crew shifts racks from propagation to finishing at another site. They scan the trays before loading them, so inventory numbers are adjusted immediately. The receiving site knows what is coming before the truck arrives.
- A customer calls to ask about the order status. Instead of calling around, your team looks up live data from any device to confirm how many racks are ready and where they are.
Without mobile tools, each step would require more calls and increase the room for error.
Look For Offline Options
Some greenhouses have weak Wi-Fi. Good greenhouse inventory apps also work offline. Staff can scan racks or adjust counts without losing data if the signal drops. The system syncs once the connection comes back.
This stops lost scans and wrong numbers when workers move between greenhouses or fields.
Barcodes And Scanning Speed
Mobile tools should handle barcode scanning easily. Many nurseries use serialized trays. Fast, simple scanning keeps inventory up to date without manual data entry.
When you buy greenhouse software, check that scanning is smooth. Staff should not waste time typing numbers for every rack. This slows work and causes mistakes.
Reduce Plant Loss
Mobile updates enable growers to maintain better control over their plants at each stage. If something goes wrong on one site, managers shift healthy plants to other orders or locations. Slow updates make that harder.