Weigh Modules in Industrial Weighing: How They Work and Where to Use Them
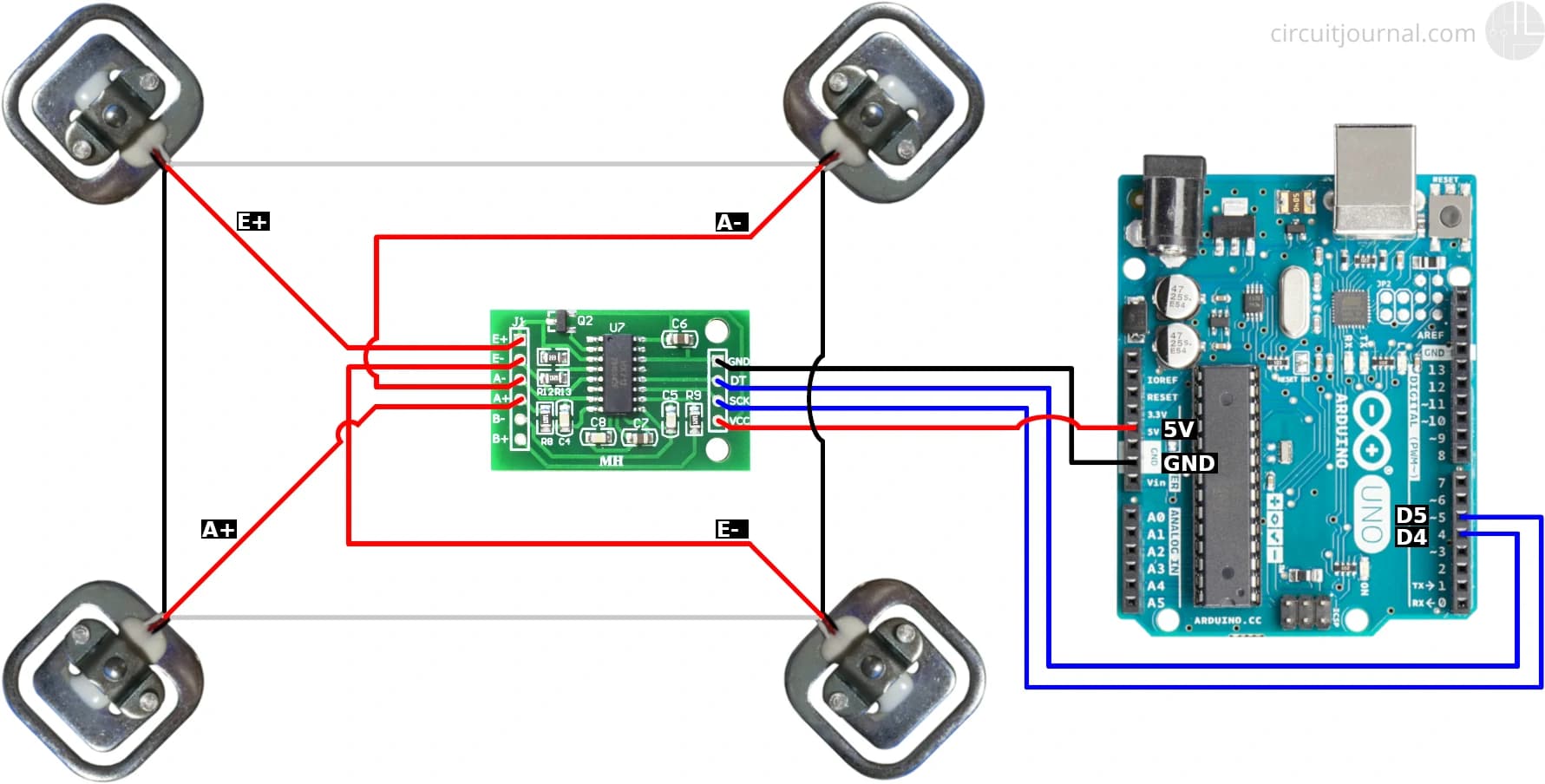
In the world of industrial manufacturing, logistics, and process automation, precision is critical—especially when it comes to weight measurement. One of the most efficient and reliable tools used for this purpose is the weigh module. These components enable highly accurate weight sensing in a wide variety of setups, including tanks, hoppers, silos, and conveyor systems. Their compact design and adaptability make them a preferred choice for engineers and facility managers looking to integrate or upgrade weighing capabilities in industrial environments.
Weigh modules typically consist of load cells mounted within a pre-engineered mechanical housing designed for straightforward installation and alignment. For a detailed overview of available designs, technical specifications, and common applications, the weigh modules page provides comprehensive information about how these systems are structured and where they excel.
What Are Weigh Modules?
Weigh modules are modular units that integrate load cells with mounting and stabilizing components. They serve as the foundation for many industrial weighing systems, allowing large vessels and structures to be monitored for weight changes in real-time. Rather than designing a weighing system from scratch, engineers can use weigh modules to quickly and efficiently convert existing structures into high-precision scales.
Each weigh module typically includes:
- Load Cell: The sensor that measures the applied force or load and converts it into an electrical signal.
- Mounting Assembly: A mechanical framework that secures the load cell and allows for thermal expansion, vibration isolation, and safe load transfer.
- Alignment and Restraint Features: These include devices such as bump stops, rocker pins, or anti-lift mechanisms that keep the system stable during operation.
How Do Weigh Modules Work?
The working principle of a weigh module is based on the load cell, which uses strain gauge technology to detect force. When weight is applied to a structure supported by weigh modules, the load cells inside detect the mechanical deformation. This deformation causes a change in the electrical resistance of the strain gauges, which is then translated into an output signal. This signal is processed by weighing indicators or control systems to display the weight or trigger actions like filling, batching, or alerting.
Because weigh modules are often subjected to environmental stresses—such as vibration, temperature changes, and lateral forces—they are designed to mitigate these effects. This ensures that the output remains accurate and stable over time, even under dynamic or uneven loading conditions.
Industrial Applications of Weigh Modules
Weigh modules are highly versatile and are used in a wide variety of industrial environments. Some of the most common applications include:
Tank and Hopper Weighing
Tanks used in chemical processing, food manufacturing, or pharmaceuticals are often mounted on weigh modules to monitor material levels, measure input/output, and support recipe-based batch control systems.
Silo and Bin Weighing
Bulk storage silos are commonly fitted with weigh modules to monitor inventory levels, enabling real-time data for logistics, production planning, and material handling.
Mixing and Batching Systems
In automated manufacturing, weigh modules are essential for ensuring the correct proportions of ingredients are combined. They are used in batch reactors, blending systems, and dosing stations.
Conveyor and Material Handling Systems
Weigh modules can also be used under conveyor systems to track the weight of goods in motion, supporting process control, quality assurance, and load distribution monitoring.
Custom Machinery and OEM Equipment
Machine builders integrate weigh modules into specialized equipment for packaging, filling, and inspection. Their modular nature and standardized outputs make them easy to design into existing or new systems.
Benefits of Using Weigh Modules
High Precision and Reliability
With proper calibration and installation, weigh modules provide highly accurate measurements even in tough industrial environments.
Easy Installation and Maintenance
Pre-engineered mounting solutions reduce installation time and help avoid misalignment errors. Most systems require minimal maintenance once installed.
Scalability
Weigh modules can be used in systems ranging from small laboratory tanks to massive industrial silos, offering a scalable solution to fit different load requirements.
Durability
Constructed from materials like stainless steel or alloy steel and often sealed against moisture and dust, weigh modules are built for long-term use in demanding settings.
Safety and Stability
Integrated safety features like anti-uplift protection and lateral restraints ensure operational safety, especially when dealing with large or elevated vessels.
Choosing the Right Weigh Module
When selecting a weigh module, consider the following factors:
- Load Capacity: Ensure the module supports the total load with appropriate safety margins.
- Environmental Conditions: Choose modules with protection ratings suitable for temperature, moisture, and chemical exposure.
- Accuracy Requirements: Match the system’s precision to your operational needs.
- Mounting Configuration: Evaluate installation space and movement allowances such as thermal expansion or vibrations.
Factors to Consider When Selecting a Load Cell
Before choosing a steel double ended shear beam load cell for your project, consider the following factors:
- Load capacity range: Ensure the load cell meets or exceeds your application’s maximum load requirement.
- Environmental exposure: Select models with appropriate sealing for dust, moisture, and temperature variations.
- System compatibility: Verify electrical output compatibility with your indicators or data acquisition system.
- Mounting options: Choose the appropriate mounting hardware for ease of installation and system stability.
Conclusion
Weigh modules have become a cornerstone of industrial weighing systems due to their accuracy, adaptability, and ease of integration. From tank weighing in process plants to inventory tracking in silos and bins, these systems provide real-time insights into material flow and production efficiency. By selecting the right weigh module and installing it correctly, businesses can achieve greater control over their processes, reduce waste, and improve overall productivity.