Considerations Before Designing A Cable Harness
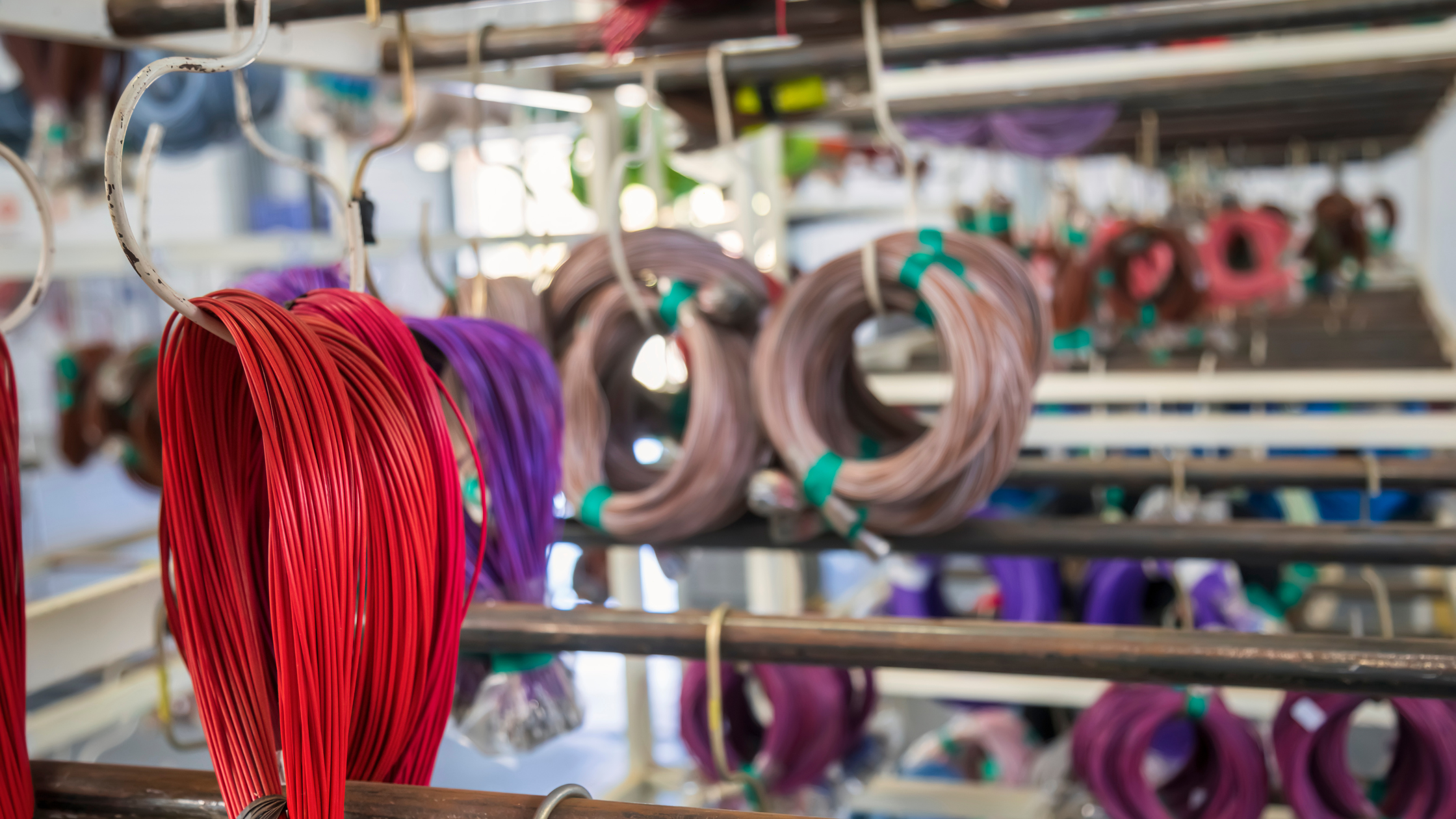
When it comes to designing a cable harness, one of the first steps is choosing a reliable cable harness manufacturer that understands the technical and logistical complexities involved in the process. The importance of an efficient cable harness cannot be overstated, especially in industries like automotive, aerospace, and industrial machinery, where high performance and safety are paramount. A well-designed cable harness plays a critical role in ensuring that electrical systems operate smoothly, minimizing the risk of system failures and improving the overall efficiency of equipment.
In India, with the increasing demand for sophisticated electronic and electrical systems across various sectors, understanding the crucial elements of designing a cable harness is essential. Whether you’re in automotive manufacturing, robotics, or renewable energy systems, the considerations before designing a cable harness will directly impact the quality and functionality of the final product. Let’s explore the key factors you need to consider before embarking on this process.
Understanding the Purpose and Application
The first consideration when designing a cable harness is understanding the application and purpose for which the harness will be used. This step involves recognizing the environment in which the cable harness will operate. Will it be used in an automotive system, an industrial machine, or perhaps in medical devices? Each application has its own set of requirements in terms of size, flexibility, and durability.
For example, automotive cable harnesses require flexibility to navigate through tight spaces within the vehicle, while industrial cable harnesses need to withstand vibrations, heat, and potentially harsh chemicals. Understanding these factors will determine the materials used, the design specifications, and the overall construction of the cable harness.
Selecting the Right Materials
Cable harness design is heavily influenced by the choice of materials. The cables, connectors, and protective covers must all be chosen with care. The primary materials used in cable harnesses include copper for wiring, rubber or PVC for insulation, and various metals and plastics for connectors and enclosures.
The material must be able to withstand environmental factors such as extreme temperatures, moisture, chemical exposure, and mechanical stress. Additionally, the cable’s insulation must be chosen based on whether the system will be exposed to electromagnetic interference (EMI) or radio-frequency interference (RFI). For industrial applications, where reliability is key, using high-quality, durable materials is essential to avoid premature failures.
Designing for Space and Weight Constraints
Another crucial consideration when designing a cable harness is the available space and weight constraints. In industries such as aerospace, space is often limited, and the cable harness must be designed to fit into tight areas without compromising the integrity of the electrical systems.
In automotive and aviation applications, reducing weight is just as important. A heavy cable harness can add unnecessary weight to the vehicle or aircraft, reducing fuel efficiency and performance. As a result, lightweight materials must be considered for the wiring and connectors. The design process should involve careful planning to ensure that the cable harness does not add unnecessary bulk or weight to the system.
Understanding Electrical Load and Power Requirements
The electrical load carried by the cable harness is another important factor to consider. The cables and connectors must be capable of handling the power requirements of the system without causing overheating or power losses. Overloading a cable harness can result in damaged wiring, system failure, and even safety hazards.
Therefore, it’s important to consider the voltage, current, and resistance specifications of the system when selecting cables and connectors. The cable gauge must be suitable for the power being transmitted, and connectors should have the right amperage rating to avoid power loss and ensure optimal performance.
Ensuring Proper Cable Routing
Cable routing is often a challenging aspect of cable harness design. Proper routing ensures that the cables are protected from damage caused by abrasion, tension, or sharp edges. The routing should be designed to minimize the potential for wear and tear, as well as avoid interference with moving parts or other systems within the equipment.
In vehicles, for example, cables must be routed to avoid exposure to heat from the engine or moving parts like wheels. Similarly, in industrial machines, cable routing should avoid interference with mechanical movements and maintain proper cable tension to ensure smooth operation.
Designing for Durability and Reliability
The durability and reliability of a cable harness are paramount, especially in high-stakes industries like aerospace and medical devices. A harness that fails prematurely can result in system malfunctions, costly repairs, and even safety risks. The cable harness should be designed with longevity in mind, using materials that can withstand the wear and tear of daily use.
Regular testing and quality assurance checks must be implemented to verify the durability of the cable harness. In addition to physical durability, the electrical integrity of the harness should also be tested to ensure that the connections are secure and capable of transmitting power without degradation over time.
Compliance with Standards and Regulations
The final consideration when designing a cable harness is ensuring that the harness complies with relevant industry standards and regulations. In many industries, such as automotive, aerospace, and medical, strict guidelines govern the design and manufacturing of cable harnesses.
These standards cover everything from the materials used in the harness to the performance of the finished product. In India, cable harness manufacturers must comply with the Indian Bureau of Standards (BIS) and international standards such as ISO 9001 and UL certifications. Compliance not only ensures that the harness meets quality and safety standards but also helps manufacturers avoid legal and operational issues.
Cost and Budget Considerations
Designing a cable harness that balances performance with cost efficiency is crucial for many businesses. While high-quality materials and advanced design may increase the initial cost, they can save money in the long run by reducing maintenance needs and preventing system failures.
However, it’s essential to find a balance between cost and quality. Understanding the budget constraints and exploring cost-effective solutions without compromising the reliability or performance of the cable harness is a key aspect of the design process.
Conclusion
Designing a cable harness is a complex process that requires careful consideration of various factors, including the purpose of the harness, the materials used, space and weight constraints, electrical load, routing, durability, compliance with standards, and cost considerations. By keeping these considerations in mind, businesses can create cable harnesses that are reliable, efficient, and capable of meeting the demanding needs of modern electrical systems.