Copper Pin-Holes: Understanding Their Impact on Electronics Manufacturing
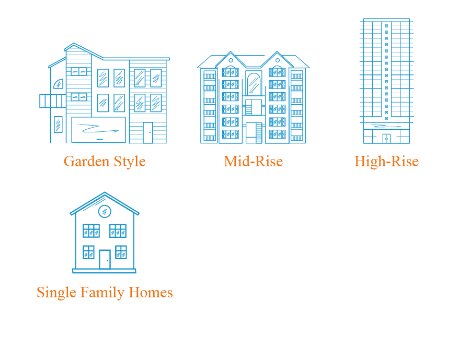
Copper pin-holes are a significant concern in the realm of electronics manufacturing, especially in the production of printed circuit boards (PCBs). These small defects can have far-reaching consequences on the performance and reliability of electronic devices. This article delves into the nature of copper pin-holes, their causes, implications, detection methods, and strategies for prevention and remediation.
What Are Copper Pin-Holes?
Copper pin-holes are microscopic voids or holes in copper layers used in electronic components, typically measuring less than 100 micrometers in diameter. They can occur during various stages of the manufacturing process, particularly during electroplating and etching. The presence of pin-holes can compromise electrical connections, leading to malfunctions and failures in electronic devices.
The Manufacturing Process and Pin-Hole Formation
The manufacturing process for PCBs involves several key stages, each of which presents opportunities for the formation of copper pin-holes:
- Electroplating: This process involves depositing a layer of copper onto a substrate. If the electroplating solution is improperly mixed or if there are fluctuations in current density, it can result in insufficient copper deposition, leading to pin-hole formation.
- Etching: During the etching phase, unwanted copper is removed to create circuit patterns. If this process is not uniform, it can leave behind voids, leading to pin-holes in the copper layer.
- Surface Preparation: Proper cleaning and preparation of surfaces are critical before plating. Contaminants, residues, or inadequate surface treatment can hinder copper adhesion and increase the likelihood of pin-holes.
- Lamination: The lamination process can introduce mechanical stresses that may contribute to the formation of pin-holes.
Causes of Copper Pin-Hole Formation
Understanding the root causes of copper pin-holes is essential for manufacturers aiming to minimize defects. Several factors contribute to their formation:
- Chemical Composition: The formulation of the electroplating solution is crucial. Impurities or incorrect concentrations can lead to non-uniform copper deposition, creating conditions conducive to pin-hole formation.
- Temperature Variations: Fluctuations in temperature during the manufacturing process can impact the electroplating and etching processes, leading to inconsistent copper layers and pin-holes.
- Current Density Issues: Uneven current distribution during electroplating can result in areas where copper is inadequately deposited, creating pin-holes.
- Mechanical Stress: Mechanical forces from handling or processing can introduce cracks or separations in the copper layer, leading to pin-hole development.
- Surface Contamination: Contaminants on the substrate can interfere with proper copper adhesion, increasing the risk of pin-hole formation.
Implications of Copper Pin-Holes
The presence of copper pin-holes can lead to several critical issues:
- Electrical Failures: Pin-holes can create short circuits or open circuits, significantly affecting the reliability and performance of electronic devices, particularly in high-stakes applications like aerospace and medical devices.
- Corrosion: Pin-holes can expose underlying materials to moisture and contaminants, leading to corrosion over time. This degradation can further compromise the integrity and lifespan of electronic components.
- Increased Manufacturing Costs: The need to detect and repair defects can elevate manufacturing costs and prolong production timelines. In competitive markets, this can hinder profitability and market share.
- Reduced Product Lifespan: Products that exhibit pin-hole defects may have shorter operational lifespans, resulting in higher warranty claims and diminished customer satisfaction.
- Regulatory Compliance Issues: In industries where reliability and safety are paramount, pin-hole defects can lead to non-compliance with regulatory standards, which can result in costly penalties and reputational damage.
Detection Methods for Copper Pin-Holes
Identifying copper pin-holes is vital for ensuring high-quality manufacturing. Various detection methods can be employed:
- Visual Inspection: While effective for identifying larger defects, visual inspections often fail to detect microscopic pin-holes.
- X-ray Inspection: This non-destructive method provides detailed imaging of internal structures, effectively revealing pin-holes.
- Electrical Testing: Techniques such as electrical resistance testing can help identify pin-holes by measuring circuit conductivity.
- Scanning Electron Microscopy (SEM): SEM offers high-resolution imaging, allowing for precise detection and analysis of pin-holes.
- Automated Optical Inspection (AOI): Advanced AOI systems utilize high-resolution cameras and sophisticated image processing algorithms to detect surface defects, including pin-holes.
Preventing Copper Pin-Holes
Preventive Pinhole leak measures are crucial for maintaining the quality and reliability of electronic components. Here are several strategies manufacturers can implement:
- Optimizing Plating Solutions: Regular monitoring and adjusting the chemical composition of electroplating solutions can help achieve uniform copper deposition.
- Temperature Control: Maintaining consistent temperatures throughout the manufacturing process can prevent variations that lead to pin-hole formation.
- Enhancing Surface Preparation: Thorough cleaning and treatment of surfaces before plating can improve copper adhesion and reduce the likelihood of defects.
- Monitoring Current Density: Implementing controls to ensure even current distribution during electroplating can significantly minimize the occurrence of pin-holes.
- Quality Control Protocols: Establishing robust quality control measures throughout the manufacturing process can help identify and address potential issues before they result in defects.
- Staff Training and Education: Providing training for employees on best practices in handling materials and equipment can help minimize mechanical stresses that contribute to pin-hole formation.
Addressing Existing Copper Pin-Hole Defects
When copper pin-holes are detected, prompt intervention is critical. Here are some potential solutions:
- Repair Techniques: Depending on the severity of the defects, methods such as re-plating or applying conductive epoxy can be employed to repair affected areas.
- Rework Processes: In some cases, defective components can undergo rework to correct pin-hole issues before they reach the market.
- Rejection of Defective Units: If pin-holes leak compromise product integrity, rejecting defective units may be necessary to ensure high-quality delivery.
- Implementing Feedback Loops: Establishing processes to learn from defects can help improve manufacturing practices and reduce future occurrences of pin-holes.
Industry Case Studies
To illustrate the impact of copper pin-holes, consider these case studies:
- Consumer Electronics: A leading smartphone manufacturer faced production delays due to high rates of copper pin-holes in their PCBs. By enhancing their electroplating process and implementing stricter quality control measures, they significantly reduced defect rates, leading to improved production efficiency and product reliability.
- Automotive Sector: An automotive company discovered that copper pin-holes in their electronic control units were causing intermittent failures. By investing in advanced detection technologies and refining their manufacturing processes, they were able to identify and rectify defects before components were assembled into vehicles, reducing warranty claims and enhancing customer trust.
Conclusion
Copper pin-holes are a critical challenge in electronics manufacturing, with the potential to compromise product reliability and performance. Understanding their causes, implications, and detection methods is essential for manufacturers aiming to maintain high quality. By implementing preventive measures and effective solutions for addressing existing defects, companies can enhance the reliability and longevity of their products. As technology continues to evolve, addressing these microscopic defects will remain a priority for manufacturers striving for excellence in the electronics industry.
Investing in quality control, staff training, and advanced detection methods will not only mitigate the risks associated with copper pin-holes but also contribute to a stronger reputation and greater customer satisfaction.