3D Printed Houses in Georgetown TX: Paving the Way for Green Housing
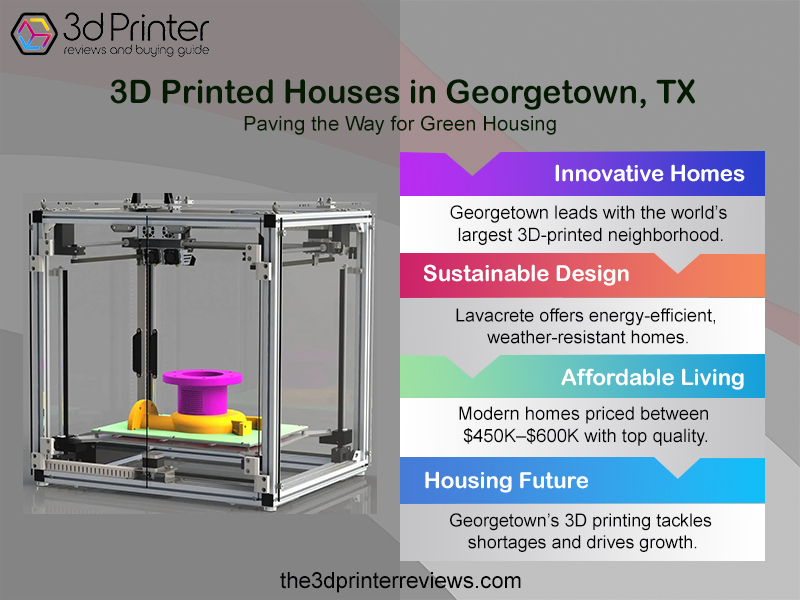
Investing in 3D printing technology is becoming a smart move—especially for small business owners looking to cut costs and boost efficiency.
A great example comes from Georgetown, Texas, where a groundbreaking project is changing how homes are built. The city is creating Wolf Ranch, the world’s largest 3D-printed neighborhood, with 100 single-family homes printed using ICON’s Vulcan printer.
This project shows just how powerful 3D printing can be in real estate. It saves time, reduces waste, and lowers construction costs. For beginners in the industry, this proves that even small startups can tap into big opportunities. Choosing the best 3D printer for small business can help you enter this fast-growing market with minimal overhead and maximum creativity.
Prologue to 3D-Printed Housing in Georgetown, TX
Overview of Georgetown’s Innovative Approach to Homebuilding
Georgetown, Texas, is at the forefront of modern construction with its innovative approach to homebuilding. The city is developing 3D-printed houses in Georgetown TX through the Genesis Collection at Wolf Ranch.
This project, a collaboration between ICON, Lennar, and Hillwood Communities, aims to construct 100 homes using advanced 3D printing technology.
The homes are built using ICON’s Vulcan printer, which layers a concrete mixture to construct the house, offering faster, more cost-effective construction.
The homes are designed to be resilient against extreme weather, water, mold, and termites, providing excellent insulation.
The 3D-printed houses in Georgetown, TX, are priced between $450,000 and $600,000, and strong demand has already been seen. Georgetown’s integration of 3D printing represents a forward-thinking approach that could revolutionize the construction industry.
Significance of 3D Printing in Modern Construction
Integrating 3D printing into construction is changing the way we build—making it faster, more affordable, and more creative. A standout example is the rise of 3D printed houses in Georgetown TX, where homes are completed in record time with reduced labor and material waste.
This technology cuts construction costs and speeds up the entire process. It also allows for custom designs, so no two homes need to look the same. Builders can create sleek, modern styles with much more freedom than traditional methods allow—especially when using the Best Continuous 3D Printer for uninterrupted, high-quality output.
On top of that, 3D printing is eco-friendly. It uses sustainable materials and supports energy-efficient designs. The 3D printed houses in Georgetown TX prove this approach can help solve housing shortages while building smarter, greener neighborhoods.
The Genesis Collection at Wolf Ranch: A Pioneering 3D-Printed Community
Partnership Between ICON, Lennar, and Hillwood Communities
A groundbreaking housing project is taking shape in Georgetown, Texas, thanks to a powerful collaboration between ICON, Lennar, and Hillwood Communities. Together, they’re building the largest 3D-printed neighborhood in the U.S., setting a new standard in home construction.
Innovative 3D Printing Technology
At the core of this project is ICON’s advanced Vulcan printer and proprietary Lavacrete material. These tools make construction faster and the structures more durable, forming the foundation of the 3D printed houses in Georgetown TX.
High-Quality, Modern Homes
Lennar brings modern design and craftsmanship to the project. Homebuyers can choose from eight unique floor plans, each offering three to four bedrooms, with options for two or three bathrooms. Every detail reflects quality and style, combining Texas ranch-style charm with a modern twist.
A Sustainable Future
Hillwood Communities is helping shape a master-planned development that prioritizes energy efficiency, long-term durability, and affordability. The goal is not just to build homes—but to create a smart, eco-conscious neighborhood for the future.
Architectural Design and Floor Plan Options
The 3D printed houses in Georgetown TX offer something truly special through the Genesis Collection at Wolf Ranch. With eight flexible floor plans ranging from 1,575 to 2,112 square feet, these homes meet the needs of modern families.
Each design includes open living spaces, spacious kitchens, smart home features, and plenty of natural light. ICON’s 3D printing technology allows for more creative layouts, combining function and form while enhancing structural integrity.
From energy-efficient materials to sleek interiors, these homes bring innovation and comfort together like never before.
Pricing Structure and Financing Options
Pricing Structure
Homes in this community start in the mid-$400,000s, with some models approaching $600,000, depending on the floor plan and features. Given their size, quality, and sustainability, 3D printed houses in Georgetown TX offer excellent value in today’s housing market.
Financing Options
Buyers can access traditional loans like conventional, FHA, or VA. Lennar also provides in-house financing, simplifying the buying process. Some local banks, already familiar with 3D-printed housing, offer flexible mortgage solutions tailored to these new homes.
The rise of 3D printed houses in Georgetown TX marks a major leap forward in how we design and build homes. With durable materials, faster construction, smart design, and eco-friendly features, this community offers a glimpse into the future of housing. Whether you’re a first-time buyer or an investor, this is an opportunity worth watching.
Technological Innovations Behind 3D-Printed Homes
ICON’s Vulcan Printer and Lavacrete Material
3D printed houses in Georgetown TX are transforming home construction by using advanced technology like ICON’s Vulcan printer and Lavacrete material. The Vulcan printer builds each home layer by layer, delivering speed, precision, and reduced waste. Lavacrete, a durable cement-based material, boosts strength while improving efficiency.
This cutting-edge system is behind the creation of the world’s largest 3D-printed neighborhood—right in Georgetown. These homes feature three to four bedrooms and are built for long-term performance, offering energy-efficient layouts and resilient structures that stand the test of time.
One of the biggest advantages of 3D printed houses in Georgetown TX is design flexibility. Lavacrete allows builders to create curved walls, creative shapes, and unique home styles that would be expensive or difficult to produce with traditional methods.
Together, the Vulcan printer and Lavacrete are setting new standards. 3D printed houses in Georgetown TX are faster to build, more affordable, and environmentally friendly. This breakthrough is not just a trend—it’s shaping the future of how we build homes in America.
Construction Process: From Printing to Final Touches
- Site Preparation
Before printing begins, the land is cleared and leveled. A solid foundation is laid to ensure the strength and stability of 3D printed houses in Georgetown TX. - 3D Printing the Structure
ICON’s Vulcan printer uses Lavacrete to build the home layer by layer. This process creates durable, energy-efficient walls for 3D printed houses in Georgetown TX with speed and precision. - Installing Traditional Components
Once the printed structure is complete, traditional elements like roofing, windows, doors, plumbing, and electrical systems are added. This step completes the basic framework of 3D printed houses in Georgetown TX. - Interior Finishing
Final touches such as flooring, cabinets, fixtures, and paint are installed, making 3D printed houses in Georgetown TX fully livable and move-in ready.
Benefits of 3D-Printed Homes in Georgetown
Feature | Affordability and Cost Savings | Sustainability and Environmental Impact | Resilience to Environmental Challenges |
Focus | Reducing construction costs and offering accessible prices. | Minimizing waste, reducing environmental footprint, and energy efficiency. | Ensuring durability and protection against environmental threats. |
Key Benefits | Efficient 3D printing methods lower construction costs, leading to more affordable homes. | Use of sustainable materials like Lavacrete, better energy efficiency, and reduced resource waste. | Stronger resistance to water, mold, termites, and extreme weather conditions. |
Technology Used | ICON’s Vulcan 3D printer, which reduces labor and material waste. | Lavacrete (cement-based material) used for construction. | Thick concrete walls created by 3D printing ensure structural integrity. |
Impact on Homebuyers | Homes are priced competitively (starting from $450,000 to $600,000) while still offering high quality. | Lower utility bills due to better insulation and minimal energy consumption. | Increased lifespan of homes due to durable, weather-resistant construction. |
Example | Genesis Collection at Wolf Ranch, priced from $450,000. | Homes designed for resource efficiency, reduced environmental footprint. | Homes that withstand Texas’ extreme weather, ensuring long-term resilience. |
Community Impact and Reception
Local Community Response to 3D-Printed Neighborhood
The rise of 3D printed houses in Georgetown TX has sparked strong interest across the local community. Many residents are optimistic, praising the project for offering energy-efficient and resilient housing. They see it as a forward-thinking solution to today’s housing challenges.
Still, not everyone is convinced. Some locals have voiced concerns about the long-term reliability of 3D printed houses in Georgetown TX. Questions about durability, maintenance, and structural safety reflect a cautious attitude toward adopting new construction technology.
The response to 3D printed houses in Georgetown TX is mixed. While many welcome innovation and progress, others remain hesitant, preferring traditional building methods until more results are seen over time.
Economic Impact on Georgetown’s Real Estate Market
The rise of 3D-printed homes in Georgetown has made a noticeable impact on the local real estate market, spurring economic growth and attracting investors.
Boosting Economic Activity and Attracting Investment
This innovative housing development has captured the attention of investors and homebuyers eager to be part of a forward-thinking project, which in turn has fueled local economic activity. Insights from Small Business 3D Printing Secrets have also helped entrepreneurs understand how to tap into this growing market.
Influencing Property Values and Market Dynamics
These modern, energy-efficient homes are helping push property values upward. Their growing demand is driving positive changes across the surrounding real estate market.
Creating Employment Opportunities and Skill Development
Construction of these homes has opened new job opportunities for the local workforce, promoting hands-on experience with advanced building technologies and skill development.
Shifting Consumer Preferences Towards Innovative Housing
Today’s buyers are showing a stronger preference for sustainable homes that feature cutting-edge technology—shaping trends across the broader housing market.
Future Prospects of 3D-Printed Housing in Central Texas
Potential for Expansion in Georgetown and Surrounding Areas
The development of 3D printed houses in Georgetown TX is revolutionizing the local housing Market. The Genesis Collection at Wolf Ranch, a collaboration between ICON, Lennar, and Hillwood Communities, leads the charge with 100 single-family homes built using advanced 3D printing technology.
This initiative addresses the need for affordable housing and positions Georgetown as a hub for innovative construction. The success of 3D printed houses in Georgetown TX has sparked interest from neighboring areas, with many looking to adopt similar technologies.
Georgetown’s proximity to Austin makes further expansion possible. This project serves as a model for sustainable, affordable housing solutions, and the region is poised for growth.
Role of 3D Printing in Addressing Housing Shortages
Innovative homebuilding in Georgetown is showing how 3D printing can help solve housing shortages by delivering affordable, efficient, and sustainable homes.
Accelerating Construction and Reducing Costs
3D printing drastically reduces construction time and labor costs. These new homes are built faster than traditional methods, helping meet growing demand more quickly.
Enhancing Sustainability
This technology minimizes material waste and boosts energy efficiency. It supports environmentally friendly construction—an important step in building a sustainable future.
Addressing Labor Shortages
With fewer skilled workers available, 3D printing helps automate much of the building process. This reduces reliance on manual labor while keeping quality high.
Providing Affordable Housing
Lower building costs allow developers to offer homes at more affordable prices. This opens the door to homeownership for more people in the community.
Exploring Future Potential
The success of this project shows how 3D printing can be scaled to address housing needs nationwide. Innovation and speed are driving a smarter way to build.
This modern approach is reshaping the housing market—making homes faster to build, more sustainable, and within reach for more families.
Considerations for Prospective Homebuyers
Evaluating the Investment Potential of 3D-Printed Homes
Investing in 3d printed houses in georgetown tx offers a unique opportunity to be part of an innovative housing market. The Genesis Collection at Wolf Ranch, featuring 100 single-family homes, is nearly complete, with a strong interest from buyers. These homes are priced between $450,000 and $600,000, highlighting a promising market for 3D-printed homes.
The use of ICON’s Vulcan printer and Lavacrete material helps lower construction costs and speed up building timelines, making these homes an attractive investment. Their energy efficiency and resilience to environmental challenges further enhance long-term value.
With demand rising and the potential for broader adoption, this type of housing stands out as a strong investment as 3D printing technology continues to gain momentum.
Comparative Analysis: 3D-Printed vs. Traditional Construction Methods
Cost, Time, and Quality Comparisons
3D printed houses in Georgetown TX offer significant cost, time, and quality advantages.
Cost Efficiency
The construction of 3D printed houses in Georgetown, TX is more affordable due to reduced labor costs and material waste. This streamlined process makes the homes more budget-friendly, with prices ranging from $450,000 to $600,000.
Time Savings
Using 3D printing technology, the wall structures of 3D-printed houses in Georgetown, TX, can be completed in just three weeks, drastically reducing construction time compared to traditional methods.
Quality and Durability
These homes are built with durable concrete, providing resistance to water, mold, and extreme weather, ensuring long-lasting quality and low maintenance.
3D-printed houses in Georgetown, TX, offer an innovative and efficient approach to homebuilding with cost savings, faster construction, and lasting quality.
FAQs about 3d printed houses in georgetown tx
Q. What is the cost of 3D printed houses in Georgetown, TX?
The price of a 3D-printed house in Georgetown, TX, varies between $450,000 and $600,000, depending on its size and features.
Q. How long does it take to build a 3D printed house in Georgetown, TX?
Construction of 3D-printed houses in Georgetown, TX, can be completed 2-3 times faster than traditional building methods, with wall structures finished in about three weeks.
Q. Are 3D printed houses in Georgetown, TX, durable?
Yes, these homes are built using durable materials like Lavacrete, making them resistant to extreme weather, mold, and termites.
Q. How does 3D printing technology impact the homebuilding process?
3D printing reduces labor costs, material waste, and construction time, offering a more efficient and sustainable way to build homes in Georgetown, TX.
Wrapping up
3D printed houses in Georgetown TX are revolutionizing the housing market with efficient, affordable, and sustainable solutions.
The Genesis Collection at Wolf Ranch showcases this innovation with 100 homes built using 3D printing technology. These homes are constructed 2-3 times faster than traditional methods and cost between $450,000 and $600,000. ICON’s Vulcan printer and Lavacrete material ensure durability and design flexibility.
This project addresses housing needs and positions Georgetown as a pioneer in modern construction, setting the stage for future 3D-printed housing developments..
Reads