What factors should be considered in laser machine design for metal cutting
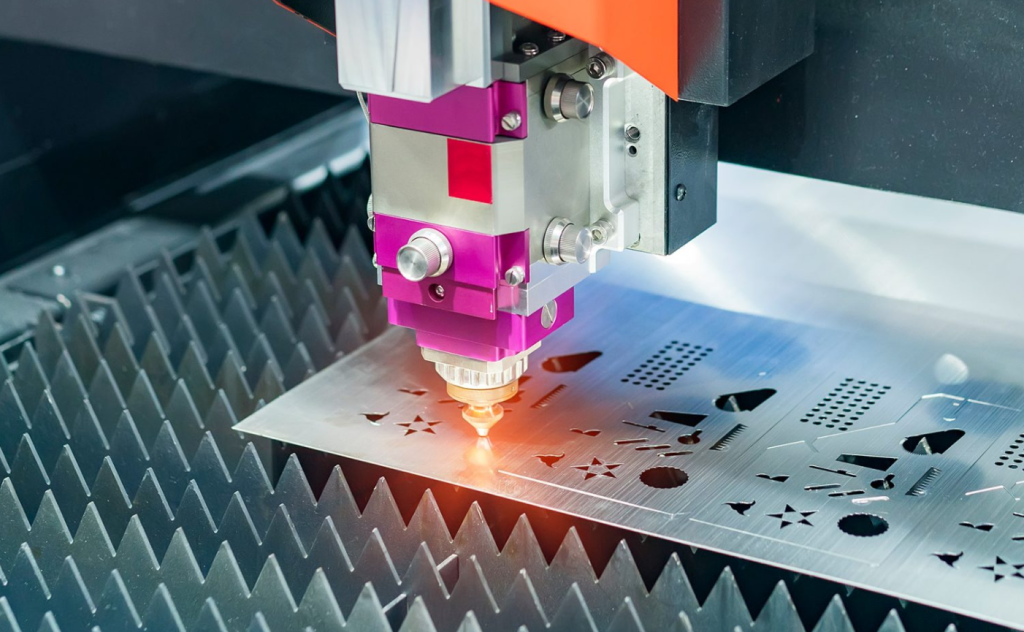
When designing a laser machine design for metal cutting, several crucial factors need to be addressed to ensure optimal performance, precision, and efficiency. Laser cutting technology has rapidly evolved, becoming a central tool in industries such as automotive, aerospace, and manufacturing. A well-designed laser machine can significantly impact the quality of the final product, speed of production, and overall operational cost. The following outlines the key aspects that influence the design of a laser machine, focusing on various components, functionalities, and considerations involved in its creation.
1. Laser Source Selection
The heart of any laser cutting machine is its laser source. This can either be a fiber laser, CO2 laser, or solid-state laser. Each type has its own set of properties that suit different applications, so the selection of the laser source is paramount in the machine design.
- Fiber Laser: Fiber lasers are known for their efficiency, precision, and versatility. They use a fiber-optic cable to transmit the laser light, which is ideal for cutting metals such as steel, aluminum, and brass. Fiber lasers offer faster cutting speeds and high-quality results, making them a popular choice in modern laser cutting machines.
- CO2 Laser: CO2 lasers are older but still widely used in cutting thicker materials. These lasers operate with a gas mixture (CO2, nitrogen, or helium) as the medium and are highly effective for cutting non-metallic materials and thicker metals. However, their cutting speed and energy efficiency may be lower than fiber lasers.
- Solid-State Lasers: These lasers are often used for high-precision applications where very fine cutting is necessary. They are typically more expensive than CO2 lasers but offer superior performance in certain scenarios, especially in intricate or delicate cutting applications.
The choice of laser source directly influences the design and capabilities of the cutting machine, affecting factors such as power output, wavelength, and beam quality.
2. Beam Quality and Focus
Beam quality is a critical factor that impacts the cutting precision and speed. The laser beam’s focus determines the width of the cut, the depth of penetration, and the heat affected zone (HAZ) of the material. In laser cutting machines, achieving the right beam quality is necessary for high-precision applications.
Laser beam quality is typically quantified using a parameter called the M² value. A lower M² value indicates a more focused and coherent beam, which allows for finer cutting. When designing a laser cutting machine, it is essential to select a laser source that can produce a beam with consistent quality and adjust it throughout the cutting process.
3. Cutting Head Design
The cutting head is the component that focuses the laser beam onto the material being cut. It plays a crucial role in the performance of the laser cutting machine. Several design considerations must be addressed to ensure that the cutting head works effectively:
- Focusing Lens: The focusing lens determines the size and intensity of the laser beam spot. The lens needs to be made from high-quality materials that can withstand the intense heat generated during cutting. Typically, a set of lenses or mirrors is used to adjust the focus dynamically during the cutting process.
- Nozzle Design: The nozzle directs the assist gas (oxygen, nitrogen, or compressed air) onto the material, helping to blow away molten metal and keep the cut clean. The nozzle must be carefully designed to avoid obstruction and maintain the proper pressure to ensure that the assist gas flows smoothly.
- Assist Gas Delivery System: The use of assist gases is essential for laser cutting. The gases, such as nitrogen or oxygen, are delivered through the cutting head and serve to remove debris, prevent oxidation, and cool the material. The nozzle and gas delivery system design must ensure the consistent and precise flow of assist gases.
4. Motion Control System
A laser cutting machine’s motion control system is responsible for moving the cutting head or the material being cut. This is a vital component in ensuring that the machine operates accurately and efficiently.
- Linear Motors and Drive Systems: High-precision linear motors and drive systems are often used in laser cutting machines. These systems must be robust, precise, and capable of delivering fast, accurate movements across the entire cutting area. The design of these motors and drives plays a major role in the overall speed and accuracy of the machine.
- Dynamic Range of Motion: Laser cutting machines should be designed with a motion range that can accommodate various material sizes and thicknesses. The motion control system must be able to precisely follow complex cutting paths while maintaining a high level of repeatability.
- Software Integration: The machine’s motion control system is integrated with software that dictates the cutting pattern and coordinates the movement of the cutting head. The software must be capable of processing complex designs and converting them into instructions that guide the machine’s movements.
5. Thermal Management
Laser cutting generates a significant amount of heat, especially when cutting thick materials. Thermal management is crucial to ensure the stability and longevity of the laser machine. Excessive heat can lead to material distortion, loss of precision, and damage to components.
- Cooling Systems: A well-designed cooling system is necessary to regulate the temperature of the laser source, cutting head, and other critical components. Cooling systems typically use water or air to maintain an optimal operating temperature and prevent overheating.
- Heat Dissipation Mechanisms: In addition to cooling systems, the machine design should include mechanisms for dissipating heat away from sensitive parts. This includes thermal barriers or heat shields that protect the machine’s components from excess heat and ensure that the cutting process remains stable.
6. Automation and Integration
Modern laser cutting machines often include automated features to improve productivity and reduce human error. Automation is essential for applications where high throughput is required, such as in mass production.
- Loading and Unloading Systems: Automated systems for loading and unloading materials can significantly reduce cycle times and increase production efficiency. These systems can handle sheet metal, plates, or even large rolls of material and feed them into the cutting machine for processing.
- Part Sorting and Quality Control: Many laser cutting machines are designed with automated sorting and inspection systems that can sort parts based on the quality of the cut or detect defects during the cutting process. Integration of sensors and cameras allows the machine to self-monitor and adjust settings in real time, ensuring that parts meet quality standards.
7. Material Compatibility
The design of the laser cutting machine must consider the types of materials that will be processed. Different metals and non-metals require different settings and laser power levels for effective cutting. A versatile laser machine design should accommodate a wide range of materials such as stainless steel, aluminum, copper, and mild steel.
- Material Thickness and Density: The machine must be capable of adjusting laser power, focal length, and cutting speed based on the thickness and density of the material. For example, cutting thicker materials requires more power and slower speeds, while thinner materials can be processed with faster speeds and lower power.
- Reflectivity and Absorption: Some metals, like aluminum, are more reflective than others, which can pose challenges for laser cutting. The laser machine must be designed to handle these materials effectively, possibly incorporating specialized components to enhance performance when cutting highly reflective materials.
8. Safety Considerations
Laser cutting machines involve high-powered lasers, which can be hazardous if proper safety measures are not in place. When designing a laser machine, safety features must be incorporated to protect operators and prevent accidents.
- Enclosures and Safety Shields: Laser machines should be housed in protective enclosures to prevent exposure to the laser beam. These enclosures are typically equipped with safety interlocks that prevent the machine from operating when the enclosure is open.
- Beam Containment: Proper containment of the laser beam ensures that it is directed only to the material being cut, minimizing the risk of accidental exposure to operators. The laser cutting machine should also include safety features to prevent accidents from the intense heat and smoke produced during cutting.
9. Energy Efficiency
Energy consumption is a significant consideration in laser machine design, particularly in industries with high-volume production. The efficiency of the machine’s energy use directly impacts its operating costs and environmental footprint.
- Power Supply and Conversion Efficiency: A well-designed power supply system can optimize the energy conversion efficiency of the laser, reducing waste and lowering operating costs. Laser machines with high power efficiency can perform more work with less energy, benefiting both the bottom line and the environment.
- Waste Heat Recovery: Some advanced laser cutting machines are designed to recover and reuse waste heat, further improving their energy efficiency. This can be particularly useful in large-scale operations where minimizing energy consumption is crucial.
Conclusion
The design of a laser machine for metal cutting involves a multifaceted approach that incorporates a variety of technical, mechanical, and operational considerations. From selecting the laser source to optimizing beam quality, motion control, and thermal management, every aspect of the machine must be designed with precision and efficiency in mind. By carefully addressing these factors, manufacturers can develop cutting-edge laser machines that offer high performance, reliability, and versatility in metal cutting applications.