What is the difference between tooling and mould?
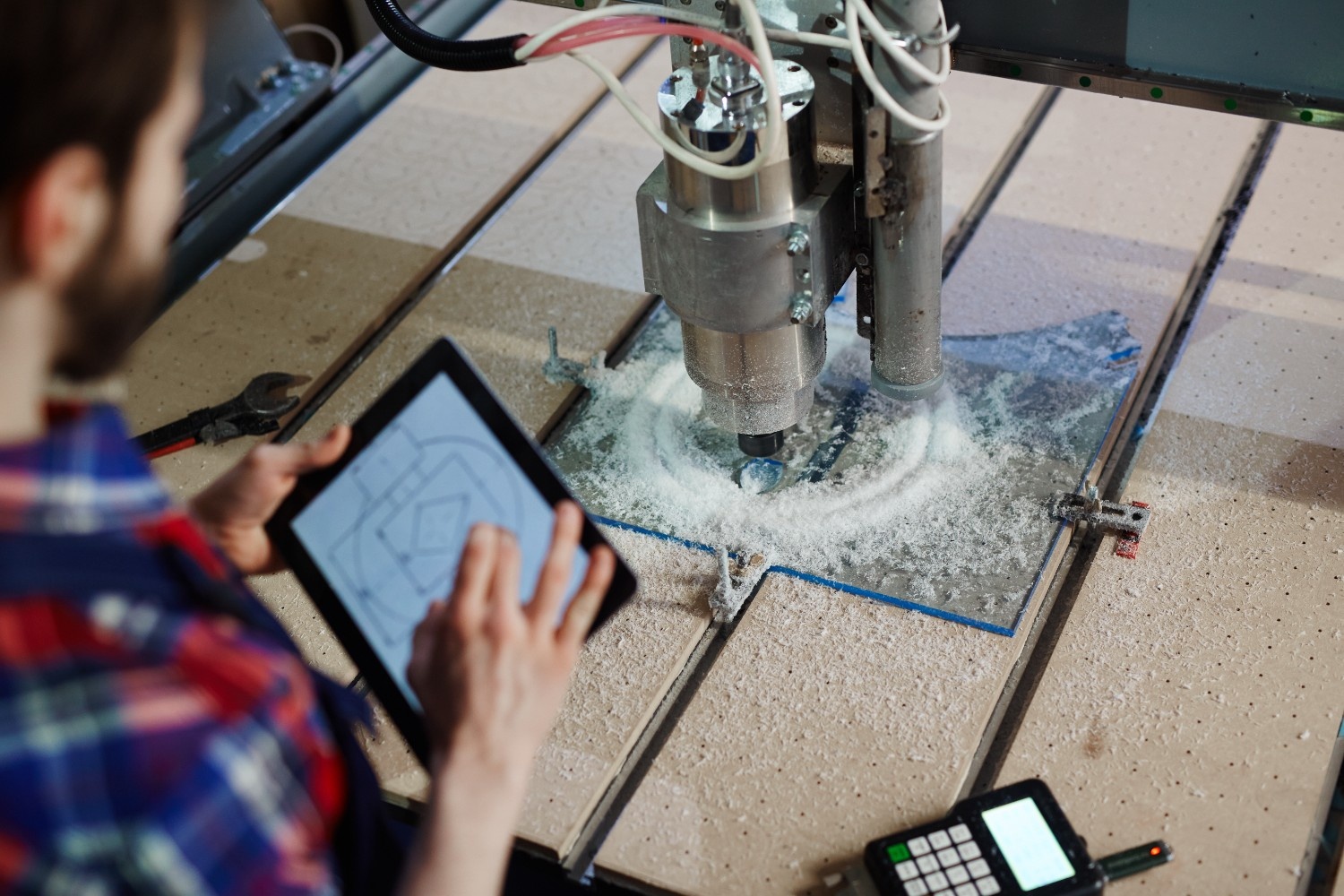
Precision in Manufacturing is a Necessity for Success in Today’s Competitive World. If you make automotive parts, medical equipment, or consumer goods, you might be asking yourself what the key difference is between moulding and moulds. In this guide, we will simplify all the important concepts which will enable you to make the right decisions for your project.
Tooling and Molds – What Are They?
PMoulds in the manufacturing industry tend to blur the lines between these two concepts, but they are in fact different and have different applications. Tooling services apply to a wider variety of equipment and processes relevant to manufacturing, as moulds are a subset of these categories.
Tooling is the compilation of equipment and tools used in the manufacturing operations, which include fixtures, jigs, dies, and other specialised equipment. Consider all the cutting tools and measuring devices, even to the complex automated systems we mentioned. In simple words, tooling is every piece of equipment necessary to transform raw material into the desired and finished goods.
Moulds, as a term, describe tools specially made to contain and shape the desired material, which is going to be kept in a predetermined shape. This process is usually used for materials which have to be heated, melted and then formed into the desired shapes.
An All-Inclusive Look at Tooling Solutions
In today’s world, food industry cutting tools are no longer limited to only one specific use. Sophisticated pieces of equipment are generated to support the ever-growing shifts in the manufacturing and production industries.
The Main Branches of Manufacturing Tooling
Exercise Documentation Training and Evaluation contains drill movements for sports, physical and rehabilitation exercises, and rehabilitation exercises for sports. Forged tool steel and tool steel cutting edges for drills with polycrystalline and cubic boron nitride have special coatings for direct edging toextend tool life.
Tools for Measurement and Inspection are of great importance to businesses focusing on defining and measuring contour cutting, such as CMM, optical measuring systems and laser measuring systems. With the ever-increasing squeezes on margins and greater sophistication of items, these tools exceed in importance.
Workholding and Fixturing Systems utilises vices, chucks, and collets and custom-made devices for holding and retaining work pieces in place during machining operations. Visord has advanced systems with modular and quick-change capabilities enabling greater flexibility.
Assembly and Testing Apparatus focuses on tools meant for the maintenance of items such as torque tools, items with press-fit and automated systems. These are vital for the maintenance of items to aid an organisation such as press-fit equipment.
Examining Mould Technology and Its Uses
Molds are an example of modMouldsngineering sophistication, enabling the accurate mass production of parts with intricate shapes and features. Along with Systems Engineering disciplines, the design and construction of amouldd requires a deep understanding of Manufacturing Engineering, Heat Transfer, and Material Science.
Injection Moulding Tooling: The Precision Standard
Injection Moulding Tooling is a sub-sector of precision manufacturing and has some of the most advanced and accurate tool configurations. The tool configurations involved in this Technique are subjected to intense pressures, high temperatures above 20,000 PSI, and severe thermal cycles, yet must remain dimensionally accurate.
In the design of injection molds, precision is a success hinges on several critical design features:
Cavity and Core Plates – define the exterior and interior shape of the parts to be formed.
Runner Systems – transport the molten plastic from the injection point to the individual cavities.
Cooling Circuits – manage temperature distribution of the tool to ensure consistent part quality and cycle times.
Elevators – remove parts without distortion post-molding.
Plastipost-moulding Mould Tooling: Engineering Excellence
Plastic injection mould tool specialists must possess knowledge on plastic materials to determine their properties, behaviour, and flow, thermal flow regarding their temperature, injection of melt, as well as cooling post moulding. The expertise required becomes more complex when dealing with multi-cavity molds, family molds, or coremould, multiple mould serialsand components.
Now engineers can use advanced simulation software to predict potential issues before constructing molds. This software reducesmouldsly changes and development time while still ensuring optimal performance right from the first production run.
Contemporary molds for plastics injectiomouldse the following hot run features:
- Hot runner systems for better material utilization and wastage preutilisation. In-mould decoration features that allow parts to be decorated while being produced.
- Insert moulding for hybrid components.
- Automatic systems for quality inspection and handling of parts.
The Most Significant Changes Brought on by Additive Manufacturing
Additive Manufacturing Tooling has disrupted the traditional tool and mold design and manufacturing process. This technology allows for the rapid prototyping of tool concepts, their intricate internal geometries, and conformal cooling channels which greatly enhance thermal management.
Tool and Mould Manufacturing Applications
3D Printers are now capable of creating functional tools with other forms of tool and molds:
Rapid Prototyping allows for fast-turnaround tools that can be created and tested for design purposes and small production batches. Conformal Cooling Inserts are specially designed for parts by custom-tailoring the cooling channels to the contours of the part, ensuring precise and effective cooling. Lightweight Fixtures engineering strives to design hollow components that are capable of supporting structures, while maintaining strength, and are low-cost in materials. Complex Assembly Jigs are used to manufacture parts with geometries that would be too costly to use traditional techniques.
The additive manufacturing approach, when combined with conventional tooling, creates advancements that are beneficial because they utilize both technologies.
Utilise Differences: Tooling Vs. Moulds – An Explanation
It will be beneficial for manufacturers to note these differences for more effective application selection:
Scope and Application Range
Tooling encompasses all processes and equipment for manufacturing. This includes but is not limited to, cutting tools, measurement equipment, and specialised automation equipspecialisedng solutions span multiple industries and processes.
Moulds use controlled cavities. Their scope includes injection molding, casting, and forging processes are limited to with the material movements the precise geometrical shapes within the cavities.
Design Complexity and Engineering Requirements
Tooling design is different for each application. Basic automation frameworks will incorporate functionality and logic rendering, while more complex automation will require sophisticated cross-disciplinary mechanical to electrical, software, and even systems-level engineering.
Mould design is all continuous. Their unique internal shapes and advanced engineering requirements demand thermal dynamic engineering along with structural analysis.
Manufacturing Processes and Lead Times
Producing tools has differing timelines based on their automation complexity. For instance, simple cutting tools may be immediately accessible while custom automation systems may require extensive months of development and testing.
Mould manufacturing has captured much of the lead time due to the processes of precision cutting, electric gathering, assembling, and verifying. For example, in the case of elaborate injectionmouldss, they require anywhere from 8-12 weeks of processing time in addition to the time for optimization and validation.
Cost Considerations and Investment Levels
Tooling costs vary significantly based on the item and service. For instance, cutting tools has simple pricing of hundreds while automation systems jump to million dollar budgets.
million-dollarnt has significantly high injection pricing. For instance it lies in the market of tens of thousands to hundreds of thousands of dollars. The value highly depends on the precision needed, complexity, and size of the item.
Choosing The Right Solution For Your Manufacturing Needs
1. Production Volume
- High-volume production justifies investment in advanced, durable tooling.
- Low-volume runs may benefit from more flexible, cost-effective tooling solutions.
2. Part Complexity & Precision
- Intricate geometries often require:
Specialised precision tools
Custom moulds and highly accurate processes
- Tight tolerances and quality standards demand enhanced tool reliability.
3. Material-Specific Cutting Tools
- Different materials require specific cutting tools:
Abrasive materials need harder, wear-resistant tools.
Using the wrong tool can lead to rapid wear or production inefficiencies.
4. Time Constraints
- Tight schedule deadlines influence the choice of tooling strategy.
- Faster tool setups may be prioritised when time-to-market is critical.
- More complex tools may offer long-term efficiency but take longer to prepare.
Innovations Within The Industry: Aprios Focusing the Attention
Move over other advanced manufacturing partners, Aprios is leading when it comes to innovation as they create everything from gears to moulds. ‘Aprios’ has the innovation when it comes to the advancements of the tools and moulds because it is backed up with technological and manufacturing proficiency that is acquired over the years and considers everything from every perspective.
Aprios has more than enough answers to other manufacturers’ questions, owing to the gap between the conservative outlook of manufacturing and the timeless ways of technologies that keep evolving. No matter the complexity in creating the tools needed for the specific client’s needs, Aprios does the entire support with effortless monitoring with guidance throughout the whole development.
The commitment from the company for the excellency is clearly visible in the systematic approach they have to the controlling over the projects and the advanced engineering support over the problems that need to be executed without problems. Pairing the diverse engineering bundle with the hands-on feel and knowledge from manufacturing helps when the needs are rough.
Trends of the Future
The equipment and tools that are being used in the manufacturing processes increase in their effectiveness, and the requirements that are used have for modern tools and devices is conditional to reach cleanliness and easiness, therefore the followed themes of molding and technologies is:
The Digital Integration expands to creating advanced tools with sensors that track and report the results in real time which makes optimization of the processes and devices of the overall system possible.
Sustainable Manufacturing utilizes processes that are recyclables, less wasteful, and more efficient.
Customization and Flexibility responds to market demands for more personalized products through flexible tooling that can quickly adapt to different configurations.
Artificial Intelligence Integration integrates automated systems that optimize tool paths, foresee necessary maintenance, and refine processes to the best preset values.
Making Informed Manufacturing Decisions
With the right information about the distinction between tooling and molds, a manufacturer is able to optimize production capabilities. Success is determined by whether you choose comprehensive tooling solutions designed for complex processes or specialized molds suitable for high-volume production.
Experienced partners who understand the technical and business goals of your project are invaluable. Accompanied by technical expertise and practical manufacturing knowledge, precision, quality, efficiency, and market demands can be met.
The best solutions are often a combination of various technologies and methodologies. Advanced manufacturers that are capable of merging traditional methods and modern changes will gain the competitive advantage intended in the market.
FAQs
1. What is the difference between tooling and mould?
Tooling includes all equipment used in manufacturing, while moulds are specific tools used to shape materials, typically in casting or injection moulding.
2. When should I choose tooling over moulds?
Choose tooling for broader manufacturing processes and automation; choose moulds for producing high volumes of parts with specific shapes.
3. What industries use moulds the most?
Moulds are commonly used in automotive, medical, packaging, and consumer goods manufacturing, especially where plastic or metal forming is required.
4. How long does it take to produce a mould?
Depending on complexity, an injection mould can take 8 to 12 weeks, including design, machining, and testing phases.
5. Are additive manufacturing tools reliable for production?
Yes, especially for rapid prototyping, conformal cooling inserts, and lightweight fixtures. They’re increasingly used alongside traditional tooling.