Top Uses for Custom Polyurethane Rollers in Manufacturing
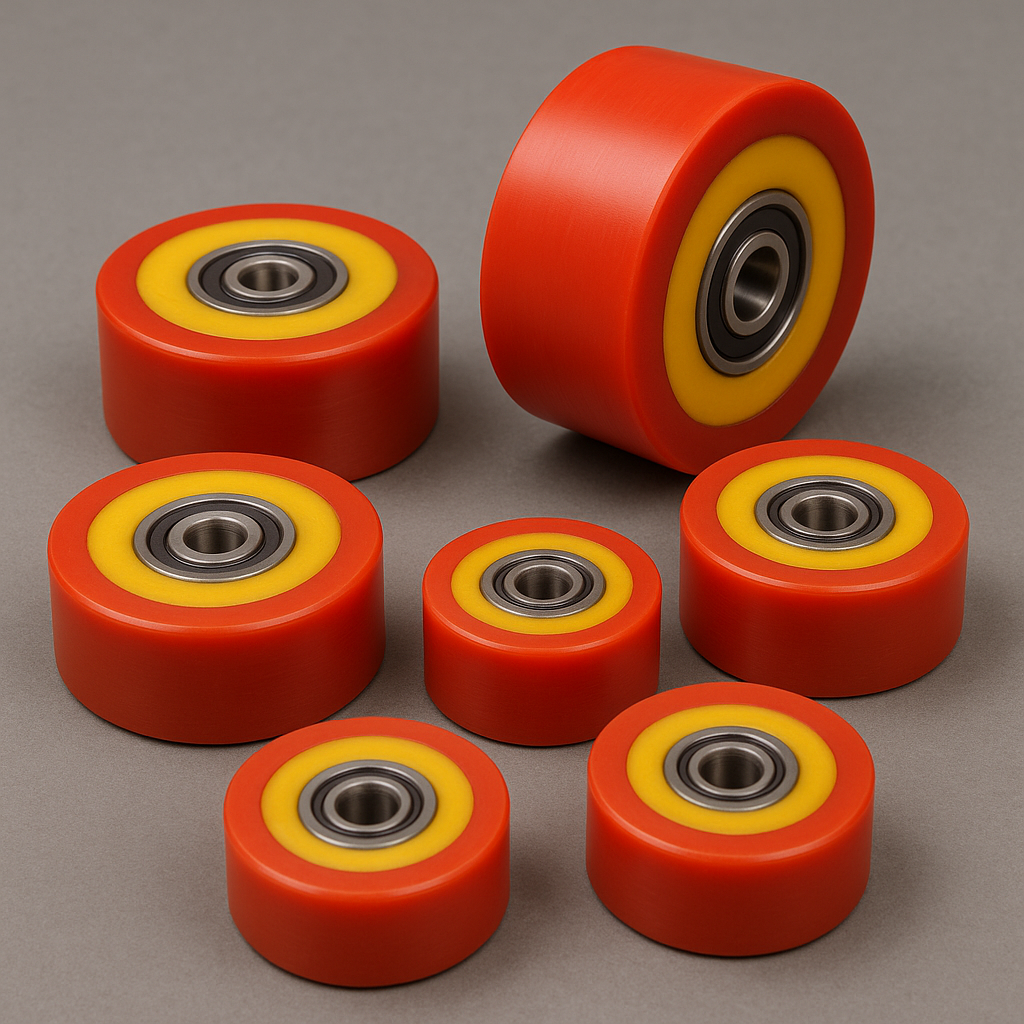
In manufacturing, efficiency depends on every moving part literally. While they may not always be the star of the show, custom polyurethane rollers play a critical role in keeping operations running smoothly. From moving parts down an assembly line to supporting heavy materials in high-speed environments, these rollers are designed to perform under pressure.
This article explores the most common industrial uses of custom polyurethane rollers, what makes them ideal for demanding environments, and how customization enhances their performance. Whether you’re optimizing a conveyor system, upgrading equipment, or specifying components for a new line, you’ll gain practical insights to guide your selection.
Why Custom Polyurethane Rollers Stand Out
Custom polyurethane rollers combine the flexibility of rubber with the strength of plastic making them a preferred choice in applications where standard materials fall short. They offer:
- Superior abrasion and wear resistance
- High load-bearing capacity
- Excellent chemical and moisture resistance
- Shock absorption and noise reduction
- Customizable hardness, geometry, and surface finish
Whether you’re looking for longevity, precision, or resilience, polyurethane rollers deliver consistent, reliable performance across a wide range of conditions.
Top Industrial Uses for Custom Polyurethane Rollers
- Conveyor and Material Handling Systems
Urethane conveyor rollers are a staple in automated manufacturing and distribution systems. Their non-marking, quiet operation makes them ideal for high-throughput lines handling delicate, packaged, or finished goods.
Why they’re used:
- Reduce noise and vibration
- Provide traction without damaging products
- Withstand high-cycle operations
- Available in custom durometers and coatings
Custom poly rollers can be tailored with grooves, flanges, or crowned surfaces to fit specific conveyor designs.
- Automotive and Heavy Equipment Manufacturing
In facilities assembling cars, trucks, or industrial vehicles, heavy duty polyurethane rollers are built into lift systems, transfer carts, and robotic arms. These environments demand components that can handle extreme weight, repeated impact, and exposure to oils and debris.
Use Cases:
- Assembly lines
- Chassis transfer systems
- AGVs (Automated Guided Vehicles)
- Welding or painting booths
Urethane coated rollers offer a balance of strength and resilience, often applied over aluminum or steel cores for added support.
- Printing, Labeling, and Packaging Lines
PU coating rollers are essential in processes where precision and surface finish matter. These rollers provide consistent contact pressure, essential for smooth printing, gluing, laminating, or cutting.
Common Applications:
- Print rollers
- Film or foil feeders
- Adhesive applicators
- Labeling systems
With excellent chemical resistance and non-stick properties, polyurethane rollers outperform rubber in high-speed, high-friction conditions.
- Wood, Glass, and Metal Processing
Processing raw materials involves sharp edges, heavy impact, and extreme heat. Here, industrial polyurethane rollers serve as feed rollers, support rollers, or drive rollers in sawmills, glass plants, and metalworking facilities.
Key Benefits:
- Prevent surface damage
- Absorb shock during cutting or stamping
- Handle abrasive materials
- Maintain performance under high loads
Custom formulations with higher hardness or heat resistance are commonly used in these settings.
- Food and Pharmaceutical Manufacturing
Cleanliness and precision are essential in regulated industries. With the right formulation, polyurethane rollers with bearings can be made FDA-compliant for direct food contact or sterile environments.
Application Areas:
- Dough rollers
- Capsule coating systems
- Cleanroom conveyors
- Packaging and sealing systems
Custom poly rollers can be designed to withstand repeated washdowns without degrading.
Custom Options That Make a Difference
When working with a qualified manufacturer, custom urethane rollers can be engineered with:
- Specific durometer (hardness) to control grip or cushioning
- Core materials like aluminum, stainless steel, or plastic
- Grooved, smooth, or crowned surfaces for different belt interactions
- Precision-machined bearings for low-friction performance
- Chemical-resistant coatings for harsh environments
Whether you need just one roller or an entire set, customization ensures your components are purpose-built not just close enough.
Trusted Manufacturers of Polyurethane Rollers
When quality and consistency matter, it’s essential to work with industry leaders. Top manufacturers like those behind Casterconcepts, Aerol, and Reaction Industries specialize in custom polyurethane rollers and wheels engineered for industrial demands.
These companies stand out for their ability to deliver:
- Application-specific engineering support
- In-house molding and machining
- Proven performance across manufacturing sectors
- Precision and repeatability for OEM and aftermarket needs
From concept to production, they offer the technical expertise and production capabilities required for custom polyurethane solutions that last.
Frequently Asked Questions (FAQ)
What makes polyurethane rollers better than rubber or steel?
Polyurethane offers better abrasion resistance than rubber and more flexibility than steel. It’s quieter, longer-lasting, and better suited for mixed industrial environments.
Are polyurethane rollers suitable for heavy duty applications?
Yes. Heavy duty polyurethane rollers are engineered to withstand extreme loads, impacts, and environmental conditions common in automotive, aerospace, and metal processing.
Can I customize the roller size, hardness, or surface design?
Absolutely. With custom polyurethane rollers, you can define the durometer, core material, shape, surface finish, and more to match your exact operational needs.
Conclusion
Whether you’re building new equipment or upgrading existing systems, custom polyurethane rollers offer a smart, high-performance solution. Their durability, customization options, and ability to handle demanding industrial environments make them a top choice across sectors.
If you’re ready to improve performance and reduce downtime, consult with a trusted manufacturer to explore custom options tailored to your application.